Fine Beautiful Info About How Do You Calculate Sensor Accuracy

Fingerprint Sensor Accuracy Graph. Download Scientific Diagram
Understanding Sensor Accuracy
1. What We Really Mean by Accuracy
Ever wondered how to figure out if that fancy new sensor you bought is actually, well, accurate? It's not as straightforward as checking if your watch matches the atomic clock (though that's a good start for some sensors!). Sensor accuracy isn't just one simple value; it's a whole collection of factors that determine how closely the sensor's readings match the real-world value it's supposed to be measuring. Think of it like trying to hit a bullseye on a dartboard. Accuracy describes how close your darts consistently land to the center, even if they aren't always exactly on the mark.
The term "sensor accuracy" is central to our discussion, and it's best understood as a noun. It represents the degree to which a sensor's output reflects the true value of what it's measuring. A sensor boasting high accuracy promises minimal deviation from reality, making it a valuable tool in various applications. This article delves into the intricacies of calculating sensor accuracy, providing you with the knowledge to evaluate and compare sensors effectively.
Now, you might think, "Why does it even matter? As long as it's close enough." And that's a fair point! The importance of accuracy really depends on the application. If you're baking a cake, a slight temperature variation might just result in a slightly denser crumb. But if you're controlling a nuclear reactor? Well, let's just say you want that temperature sensor to be spot-on. So, understanding and calculating sensor accuracy becomes crucial when precision is paramount.
Accuracy isn't everything, mind you. You also need to consider other characteristics like precision (how repeatable the readings are), resolution (the smallest change the sensor can detect), and linearity (how consistently the sensor responds across its range). But for now, let's focus on the accuracy puzzle.
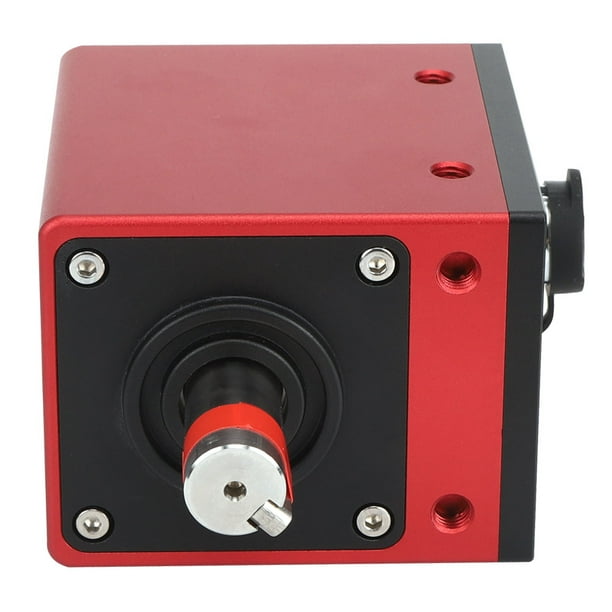
OLED Display Dynamic Torsion Sensor, Accuracy Motor Speed Sensor
Breaking Down the Components of Accuracy
2. Digging Deeper
Sensor accuracy isn't just one thing; it's a mix of different error types. We can mainly break it down into bias (systematic error) and precision (random error). Bias, sometimes called systematic error, is a constant error that shifts all measurements in the same direction. Imagine a thermometer that always reads 2 degrees too high. That's bias in action.
Precision, on the other hand, refers to the repeatability of the measurement. A precise sensor will give very similar readings when measuring the same value multiple times, even if those readings aren't necessarily accurate. Think of it like shooting a group of arrows all clustered together, but far away from the bullseye — high precision, low accuracy.
Other factors that affect accuracy include linearity (how consistently the sensor responds to changes in the measured value), hysteresis (the difference in readings depending on whether the measured value is increasing or decreasing), and temperature drift (how the sensor's readings change with temperature). Manufacturers typically provide specifications for these errors, but it's important to understand how they contribute to the overall accuracy of the sensor.
Knowing the sources of error allows you to take steps to minimize their impact. For instance, calibrating the sensor can help to correct for bias. And using sensors designed for specific temperature ranges can reduce the effect of temperature drift.

Sensor Specifications. Accuracy Is Given As A Percentage Of Each
Calculating Sensor Accuracy
3. From Data Collection to Interpretation
Alright, let's get down to the brass tacks calculating that accuracy number! There are a few common methods, and the best one depends on the data you have and what you need to know. The first step is collecting data. This involves taking multiple measurements of a known standard (something you know the true value of with very high confidence). The more measurements you take, the better your estimate of accuracy will be.
Next, you calculate the error for each measurement. The error is simply the difference between the sensor reading and the known standard value. So, if your sensor reads 25.2 degrees Celsius and the standard is 25.0 degrees Celsius, the error is 0.2 degrees Celsius. Be sure to pay attention to the sign of the error (positive or negative), as this indicates whether the sensor is over- or under-reporting.
Now, for the actual calculation! One common metric is Root Mean Square Error (RMSE). RMSE gives you an idea of the typical magnitude of the errors. It's calculated by squaring each error, averaging the squared errors, and then taking the square root of the average. Another useful metric is Mean Absolute Error (MAE), which is simply the average of the absolute values of the errors. MAE is less sensitive to outliers than RMSE.
Finally, and crucially, interpret the results in the context of your application. An RMSE of 0.1 degrees Celsius might be excellent for measuring room temperature, but completely unacceptable for a high-precision scientific instrument. Also, consider the uncertainty of your standard! Your calculated accuracy can only be as good as the accuracy of your reference point.
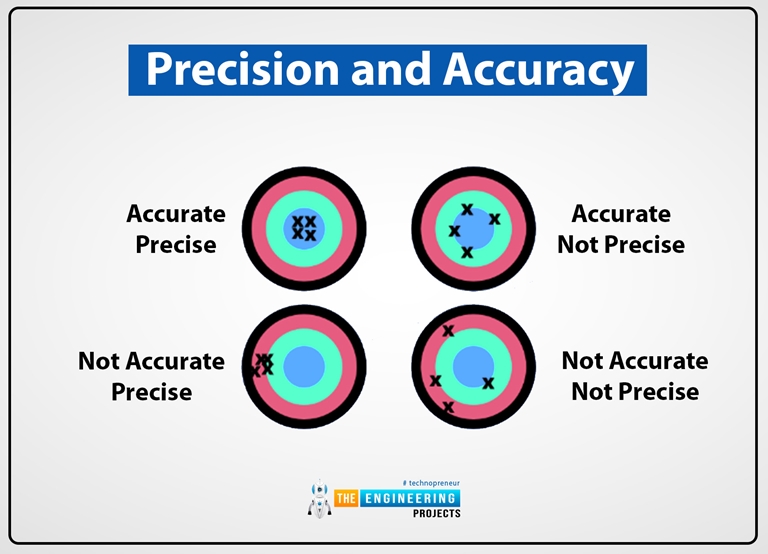
Precision And Accuracy In Physics The Engineering Projects
Practical Examples
4. Accuracy in Action
Let's look at a few examples to solidify our understanding. Imagine you're testing a pressure sensor used in a car's braking system. You compare the sensor's readings to a calibrated pressure gauge (your standard). After taking 10 readings, you calculate the RMSE to be 0.5 PSI. This tells you that, on average, the sensor's readings are off by about 0.5 PSI. Is this acceptable? It depends on the required safety margins for the braking system.
Alternatively, suppose you're evaluating a humidity sensor for an agricultural application. You compare it to a reference hygrometer (humidity meter) and find that the sensor consistently overestimates humidity by 3%. This represents a bias error. You could potentially correct for this bias by applying a correction factor to the sensor's readings. This could be done in software or even manually if the application only requires occasional readings.
Now, let's say you're comparing two different accelerometers for use in a fitness tracker. Accelerometer A has a lower RMSE but also a higher bias. Accelerometer B has a higher RMSE but a lower bias. Which one is better? Again, it depends on the application. If you're primarily interested in tracking the total number of steps taken, the lower bias of Accelerometer B might be more important. If you're interested in measuring the fine details of movement, the lower RMSE of Accelerometer A might be preferable.
These examples highlight the importance of not just calculating accuracy, but also interpreting it in the context of the specific application. Consider all the factors: bias, precision, linearity, and the uncertainty of your standard. And remember that sensor accuracy is just one piece of the puzzle. You also need to consider other factors like cost, power consumption, and reliability.
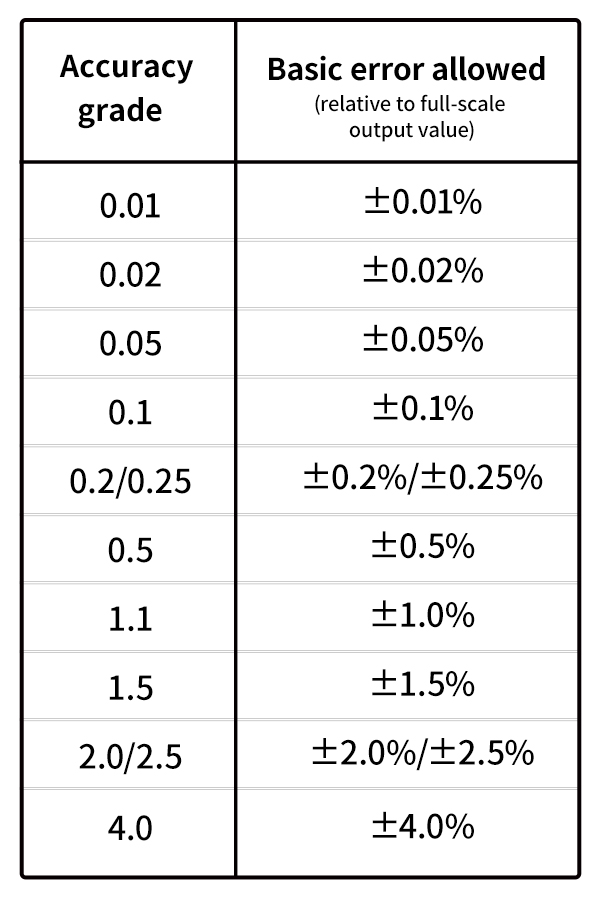
Basic Knowledge What Is The Accuracy Of Pressure Sensor?
Improving Sensor Accuracy
5. Fine-Tuning for Optimal Performance
So, you've calculated the accuracy of your sensor, and it's not quite where you want it to be. What can you do? One of the most effective methods is calibration. Calibration involves comparing the sensor's readings to a known standard and adjusting the sensor's output to match the standard. This can be done manually or using automated calibration equipment.
Another important factor is the operating environment. Sensors can be sensitive to temperature, humidity, vibration, and other environmental factors. Make sure the sensor is operating within its specified operating range. If necessary, provide shielding or insulation to protect the sensor from these factors. Also, make sure you're using the right sensor for the job. A high-precision sensor might be overkill for a simple application, while a low-precision sensor might not be accurate enough for a critical application.
Signal processing techniques can also be used to improve sensor accuracy. For example, averaging multiple readings can reduce the effect of random noise. Filtering can be used to remove unwanted signals from the sensor's output. And advanced signal processing algorithms can be used to compensate for non-linearities and other errors.
Finally, remember that sensor accuracy can degrade over time. Regular maintenance and recalibration are essential to ensure that the sensor continues to provide accurate readings. And when it's time to replace the sensor, be sure to choose a replacement that meets your accuracy requirements.
